On-road autonomous vehicles (AVs) face several well-known challenges, including pedestrian detection and path planning for situations like cut-ins, merges, and intersections. Off-road AVs face additional challenges. As they don’t operate on paved and mapped roads, off-road AVs must successfully detect traversable terrain, handle bumpy terrain, and sometimes even avoid rollovers. When testing and validating off-road AVs in simulation, development teams can address these challenges through accurate vehicle-terrain interaction modeling and, more specifically, suspension modeling.
This blog post will explain what role suspension models play in different off-road simulation use cases. Before going into these topics, this blog post will first lay out three examples of off-road autonomy use cases and how simulation enables them.
Off-Road Simulation Use Cases
Defense
According to the Congressional Research Service, 2,146 active-duty personnel in the U.S. Armed Forces have died in vehicle-related incidents during Non-Overseas Contingency Operations (Non-OCO operations) since 2006, compared to 2,723 active-duty personnel who have lost their lives during OCO operations. Autonomy can thus play a significant role in making military training and operations safer.
Autonomy plays a broad role in the defense industry, from autonomous off-road ground vehicles, such as unmanned ground vehicles (UGVs), all the way to autonomous aircraft and synthetic data generation for artificial intelligence (AI) use cases. For autonomous off-road ground vehicles, in particular, simulation assists with developing, testing, and validating the entire stack, from perception (Figure 1) and prediction to planning and controls.
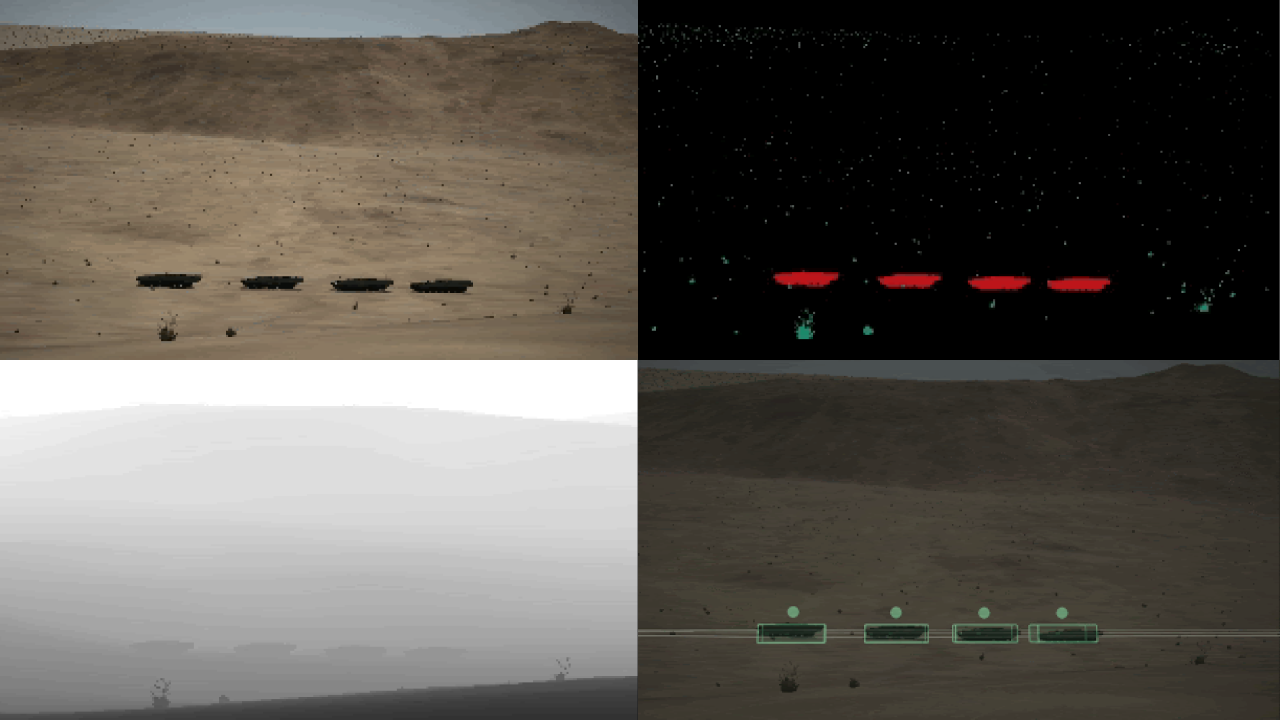
Agriculture
In the agricultural sector, functions like auto-steer have been common features for more than a decade. However, fully autonomous farming vehicles are starting to gain popularity. Examples for autonomous farming vehicles include autonomous tilling machines, combine harvesters, grain carts, and seedling planting and spraying machines. Simulation helps develop fully autonomous systems for these use cases (Figure 2) by assisting with virtual field and crop modeling, virtual vehicle modeling, and perception development.
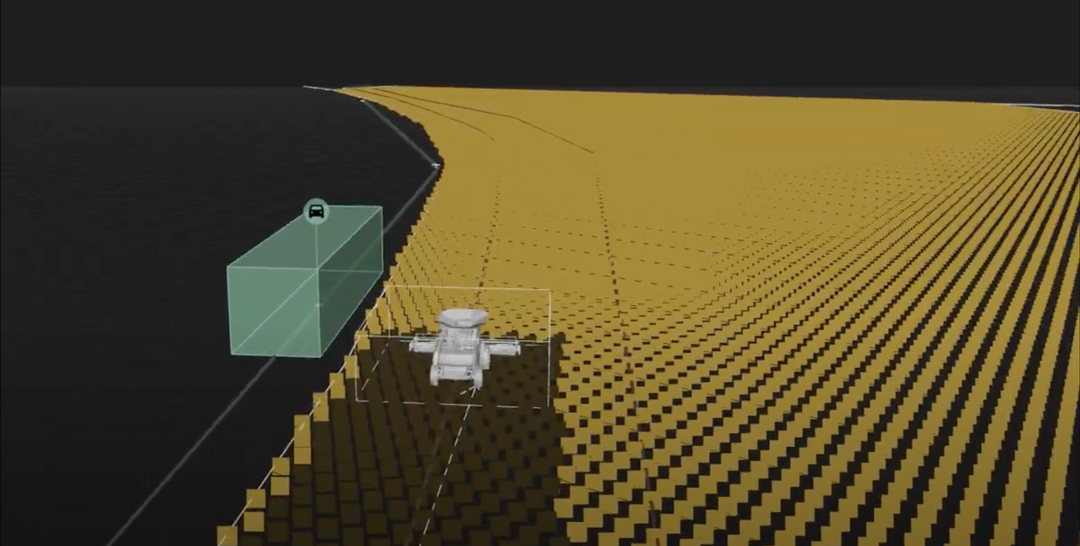
Construction and mining
The construction and mining industries use autonomous systems for various use cases such as excavation, drilling, demolition, and haulage. For each use case, simulation helps develop and test sensor models such as camera, lidar, and radar in different 3D environments, train perception algorithms to detect and avoid humans on-site, and simulate prediction, planning, and controls in multi-agent scenarios.
Importance of Suspension Models for Off-Road Simulation
Suspension models are crucial for off-road simulation because off-road vehicles often need to handle uneven terrain. Simulations that don’t account for a vehicle’s suspension might lead to results that aren’t fully representative of the real world. In particular, simulating an off-road vehicle’s suspension can have two main types of impact:
1. Impact on the AV’s perception performance
Without correctly simulating suspension, it would be difficult to study its effects on perception algorithms. It is essential to study those effects because perception stacks need to be robust and handle the additional motions induced by an AV’s suspension.
a. Pitch and roll
When driving on uneven terrain, an off-road AV’s suspension contributes to pitching and rolling motions (Figure 3) that affect the output of sensors attached to the vehicle. When the vehicle dives (i.e., pitches forward), the front-facing camera may only see the ground immediately in front of the vehicle. When the vehicle squats (i.e., pitches backward), the camera may only see the sky or surroundings located far away from the vehicle. These changes in the camera’s view may affect the output of the vehicle’s object detection algorithms, as the front-facing camera may interpret other actors or objects to be located closer or further away than they actually are.
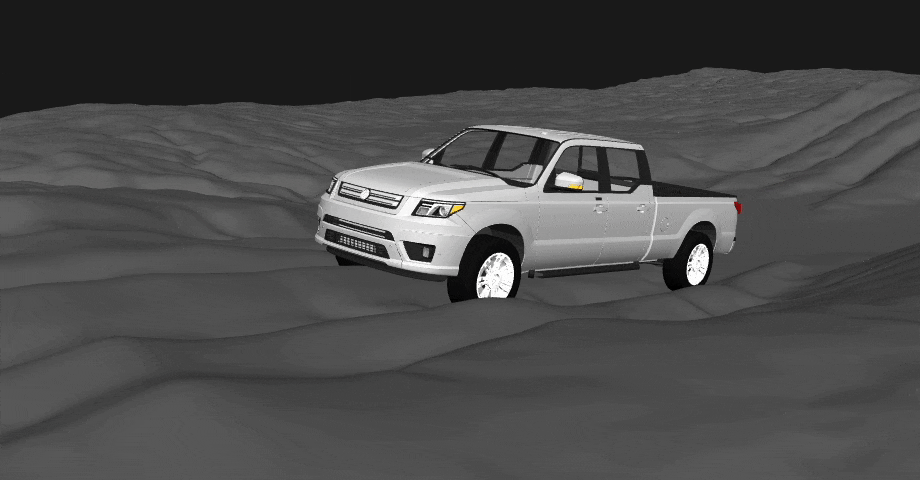
b. Sensor calibration
As an AV’s suspension affects the view and output of different sensors, those sensors must be calibrated to support either one specific suspension system or a range of different suspension systems, depending on whether the AV stack will be deployed on various vehicle models. For example, different autonomous off-road defense vehicles might use different suspension systems while using the same AV stack.
c. Interpreting actor behavior
Apart from an AV’s own vehicle suspension, the vehicle suspension of other actors is also critical to the AV’s perception performance. Machine learning algorithms in an AV’s perception stack can interpret other actors’ behaviors more accurately based on the actors’ suspension movements. For example, many perception systems learn that an actor in front of the AV is decelerating by observing the actor’s pitch. If an AV drives closely behind another actor, and that actor brakes and stops abruptly (Figure 4), the AV can detect this behavior more quickly based on the actor’s forward pitch.
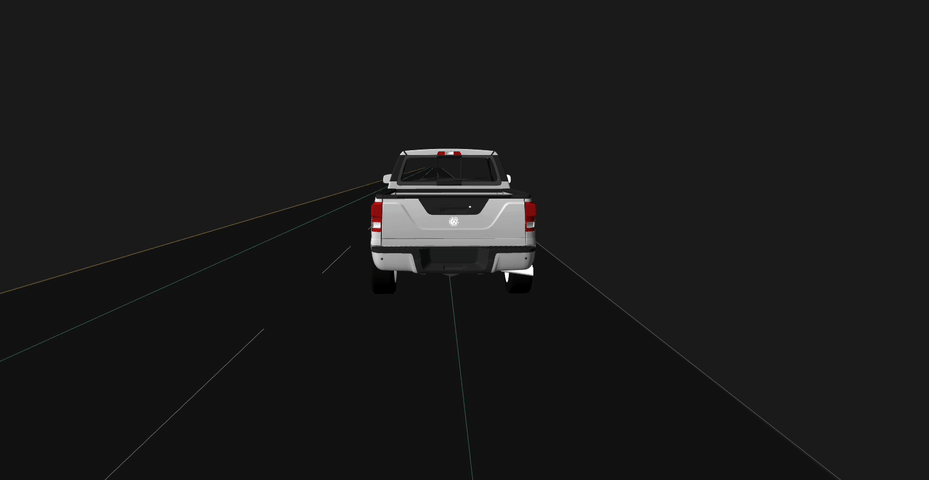
Accurate suspension models in a simulation tool allow AV development teams to train an AV’s perception algorithms to accurately handle all of the mentioned effects—from sensor movement and output to achieving the correct sensor calibration and correctly interpreting actor behavior.
2. Impact on the AV’s localization performance
The improved accuracy that comes from simulating suspension can also help improve an AV’s localization performance. An AV’s suspension causes oscillations in the vehicle, which can decrease the accuracy of the localization system by polluting the inertial measurement unit (IMU) data with noise. Simulations that incorporate suspension can simulate the effect of a suspension’s vibration modes on IMU data, and therefore provide a testbed for designing filters that remove such noise from IMU data, thereby improving the AV’s localization accuracy.
Approaches to Building Suspension Models: Different Levels of Fidelity
There are different approaches to building suspension models for simulation tools: Quarter-car, half-car, full-car, multi-body, and finite element models. While quarter-car suspension models feature low complexity and low fidelity levels, finite element models are the most complex and high-fidelity.
At first glance, it might seem like higher-fidelity suspension models enable more accurate simulations. However, this isn’t always the case. High-fidelity models come with three significant trade-offs. First, it is difficult to estimate the large number of parameters that characterize a high-fidelity suspension model. Second, running high-fidelity models requires large amounts of computing power. Third, some types of fidelity don’t add to the usefulness of a simulation tool, as there is no additional benefit to capturing the corresponding real-world nuances. For example, it isn’t necessary to factor in the deformation of tires or a vehicle’s chassis to ensure the accuracy of a vehicle’s pitching and rolling motions in an off-road or on-road AV simulation.
Applied Intuition’s Approach
We built our simulation tool Object Sim* with a level of fidelity that accurately captures the germane degrees of freedom of a vehicle’s suspension, such as pitch and roll, while still keeping the models as simple as possible.
Our team built some parts of Object Sim’s suspension models from the ground up. For other parts, the team leveraged open-source software that models a vehicle’s suspension as an abstract mass-spring-damper system without modeling the detailed linkages contained in the system. This approach is performant and captures the overall pitch and roll caused by an AV’s suspension. Modeling actual linkages in the suspension system would slow down the simulation and provide only minor improvements in terms of fidelity. While modeling the linkages would be helpful when designing a vehicle suspension system itself, its benefits are negligible in the case of off-road and on-road AV simulation.
In addition to using Applied Intuition’s vehicle suspension models, development teams can import entire vehicle models to bring their own suspension models into Object Sim. Request a product demo to learn more about vehicle suspension models in Object Sim.
If you enjoy solving AV simulation challenges like the ones discussed in this blog, apply for a role on Applied Intuition’s engineering team.
*Note: Object Sim was previously known as Simian.